From Earth to the Moon, Technology Makes Automatic House Construction Possible
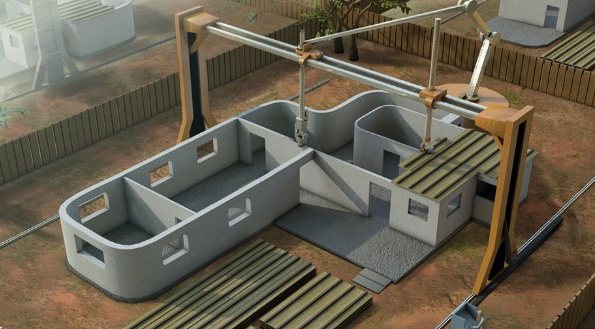
Here’s how CC works. Learn to design a condo in a computer program, prepare enough “ink” made of concrete, put it into a giant printer, and then press a button on the machine. The engine starts running and builds the condo by laying concrete on the ground layer by layer, like making a huge layer cake. Sooner or later, not only may people on Earth be able to manufacture a neighborhood in an efficient, economical way using this technology, but future astronauts on the moon and Mars may also use this technology to build human habitats.
As promising as it is, CC counts on an increasingly scarce commodity: land. If there is land to build it, it will be a great technology, said Darrell Simien, the director of real estate development at Habitat for Humanity of Greater Los Angeles.
“There is not much land for residential construction,” Simien said. “[Contour Crafting] seems to be limited to single family construction.”
Besides, Simien is also concerned whether CC will get approved by different cities as a method of construction, whether it can successfully convince the appraisals and finance institutions to finance manufacturing housing and whether it will be cost-effective while in practice.
Behrokh Khoshnevis may disagree. By shortening the project length and reducing the labor on construction site, CC may significantly reduce the cost which constitute about 70 percent of the cost of traditional construction, he said at TEDxOjai in 2012.
Khoshnevis graduated from Sharif University of Technology in Iran in 1974, and is now the director of manufacturing engineering graduate program at the University of Southern California. He spent almost 20 years coming up with the Contour Crafting concept and developing it into a prototype that can automatically build a house within 24 hours.
SEE MORE: A Link Between Viruses And Cancer
At the entrance to his office in the Andrus Gerontology Center at USC stands a small display case surrounded by glass. Inside the case there were several ceramic cylinders, flower-shaped knick-knack and a small true-to-scale house model. When I sat down with Khoshnevis, we were separated by a desk piled with books, notes, and paper. Khoshnevis, gray haired and wearing a pair of thick-framed oval glasses, sat next to his computer and a small 3D printer, typing.
When I asked about his motivation for inventing and developing CC, he sat back, put one hand on his chin and said, “It’s been my life’s mission.” He describes himself an inventor and has so far received about 20 U.S. patents and 30 International patents.
Khoshnevis considers himself an artist. On the walls around his office, paintings from his collection were on display: an oil painting of a peacock standing elegantly on a bough and a painting of vivid humming birds standing on a twig with flowers. A tier of coffee stirrers were stuck to the door of a file cabinet behind his desk. Khoshnevis designed and painted each of them with neat stripes of color.
“Art is important for the one who creates technology,” Khoshnevis said. “It stimulates the right brain and that’s where the creativity starts.”
Khoshnevis is the first one who came up with the concept of manufacturing construction via 3D printer, but 3D printing technology was initiated by Charles Hull. In 1986 Hull received the patent for the stereolithography apparatus which could produce models by curing a piece of resin with a UV laser. This became the origin of 3D printing technology. Khoshnevis said he was one of a few people who believed in its true potential at that time. In 1995, he started working on Contour Crafting project, not just to print trinkets, small parts or 3D models, but to print large-scale structures.
One of his prototypes is a six-by-six foot metal frame that consists of two cranes linked by a bar. A steel cylinder with a nozzle at the bottom hangs off the bar. Technicians and designers can use computer programs to guide the cylinder. As the machine starts working, the cylinder squeezes a thick concrete layer out through the nozzle and moves along the path. By the time the first layer of a house dries, the cylinder starts squeezing out the second layer. In this way, each wall of the house becomes higher and higher.
This prototype printed the first concrete wall, which measured three-by-three meters. Building the wall only took less than one day, but the whole process – including the design of the prototype – took about a year. During the earliest three weeks of development, Khoshnevis and his colleagues bought the nozzle, tubes and other parts to assemble a simple CC printer and tested it. On their first attempt, nothing came out.
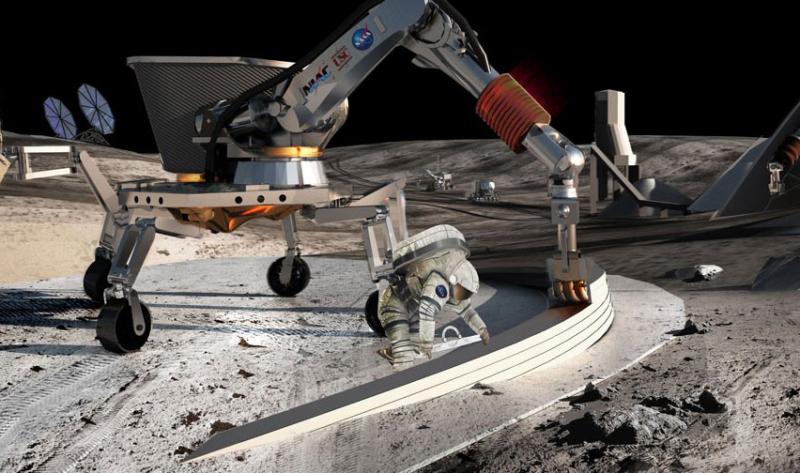
During Khoshnevis’ previous experiments, the tubes that carried the concrete often became clogged, causing constant problems. One reason was the type of concrete used: some varieties had sand and big pieces of gravel that got stuck inside of the tube. If the nozzle was too small, it wouldn’t let concrete pass through smoothly.
By the time that Khoshnevis’ team finally printed out the first wall, they had tried almost 15 different types of concrete combined with different sized nozzles. The concrete used for this wall, according to Khoshnevis, is mixed with fiber and has a strength of 10,000 pounds per square inch, while existing concrete used in houses is 2,500 to 4,000 PSI to meet the California Building Code. Generally, increasing the PSI costs extra, but CC technology can build strong walls at high speeds and at a lower cost.
Fixing clogs wasn’t the only problem; there was also timing. Ketai Yao, one of Khoshnevis collaborators in the CC research, comes from a background in engineering design and computer science. His job was to look at the geometry of the future structure and design the nozzle’s route.
Designing a house for a CC printer may be difficult for traditional architects. Because the machine prints out the building layer by layer, Yao explained, the architect has to make sure the supporting layer at the base is dry before it builds from there. The timing between laying down the base and second layer is critical because the structure may fall apart. A traditional architect, who doesn’t have enough experience with this technology, “won’t have any ideas of different layers that have to be used to do the construction,” Yao said.
Khoshnevis’ team had learned to use computer programs to accurately design the blueprint.
“Building the wall happened in one day at the end, but what leads to that is a lot of effort,” Khoshnevis said. He quoted Thomas Edison: “Invention is one percent inspiration and 99 percent of perspiration.” Then he said, nodding his head, “That’s really true.”
The one-day wall building demonstration proved CC could work. In 2004, Khoshnevis’ success began to catch a lot of attention from media. His wall-building robot has been on national TV and radio programs – CNN, ABC ScienCentral, Discovery Channel, and BBC World Service – as well as local and foreign newspapers, such as LA Times, The Age (an Australian newspaper), and Der Spiegel (a German weekly news magazine). NASA and some private companies have also shown interest in the technology’s future application.
In 2010, Khoshnevis met with A. Scott Howe, a senior systems engineer at NASA’s Jet Propulsion Laboratory whose expertise is in architecture. Khoshnevis became an outside advisor for Howe’s group which started research on how to use microwave radiation and 3D printing to build habitats in space. The group made a print head that they called a Microwave Sinterator to generate radiation to heat lunar soil, solidify it and make it a useful construction material.
“It's a very interesting technology. If it can work, you can go to the moon, you can build the city and you don't need a single person there,” said Richard Rieber, who frequently works in Howe’s group. “It will take a step further to the moon and make deep space exploration and habitation easier to do.”
In addition to Howe and Rieber, the group includes Martin Barmatz, an expert in microwave technology, Mike Seibert, a systems engineer and folks from NASA Kennedy Space Center and other team members from around the country.
Rieber started his research into powder and metallurgy when he was in college. During that time, he read a research paper that talked about using microwaves to solidify lunar soil and was inspired. After he joined JPL in 2007, he was put into contact with Seibert and Barmatz, and they tried to prove this was a workable idea.
A few years after, ATHLETE (All-Terrain Hex-Limbed Extra-Terrestrial Explorer), a six-leg, eight-meter tall robot, was designed by JPL to support human exploration of the lunar or Martian surface. Howe came up with an idea based on the concept of Contour Crafting: add a microwave sinterator to one of ATHLETE’s legs and transform the robot into a mobile 3D printer. Rieber thought the idea was “pretty slick,” and they proposed it to NASA.
According to their design, the robot will control the Sinterator as a print head to print structures – such as aircraft landing pad – with layers and layers of solidified lunar soil. This system, which combines ATHLETE with Microwave Sinterator, has received a name, Freeform Additive Construction System (FACS).
Howe said JPL would first test the robot without the Microwave Sinterator. For example, they will experiment in deserts or Antarctica to see if it will function well in sands or under extremely cold temperature.
READ MORE: California High-Speed Rail Construction To Start, Controversy Continues
But an idea isn’t enough. Now Khoshnevis and JPL are trying to raise funding for future experiments. In 2010 President Obama scrapped George Bush’s mission of returning to the moon and directed NASA to get astronauts to a near-earth asteroid by 2025. NASA lost some of its interest in lunar construction and exploration projects and has cut off its funding.
“It is a great idea. But if no one will ever go to the moon, it’s a technology with no use,” Rieber said. “Until we have the motivation, the political motivation, or frankly the commercial motivation to actually send people to the moon.”
Back on Earth, Yao said that Khoshnevis had seen his technology as one of the greatest inventions of the century. But even after so many years of steady improvement, it still has a hard time getting commercialized.
“I think the construction industry tends to be conservative,” Yao said, frowning. “Using robotics to build structures or using 3D printer to print out structures, that’s pretty radical for them.”
Khoshnevis hasn’t given up trying to commercialize his technology. He has promoted it and convinced investors for over 10 years and said he might receive funding to start his own company one of these days. His enthusiasm and endurance for his technology have brought rewards, though. In October 2014 he won a $20,000 prize in the Create the Future Design Contest for Contour Crafting, competing with 1,000 other technologies from all over the world.
“I’m comforted by the fact that people appreciate what I have gone through to create such a thing,” he said.
“You feel this strong stage to put more of yourself into it and push it forward as much as you can, so that at least you see some of it happen in your lifetime.”
Reach Contributor Xinyi Huang here. Follow the Science Desk on Twitter here.